April 15th
Unlocking the Potential: Understanding Palletizers
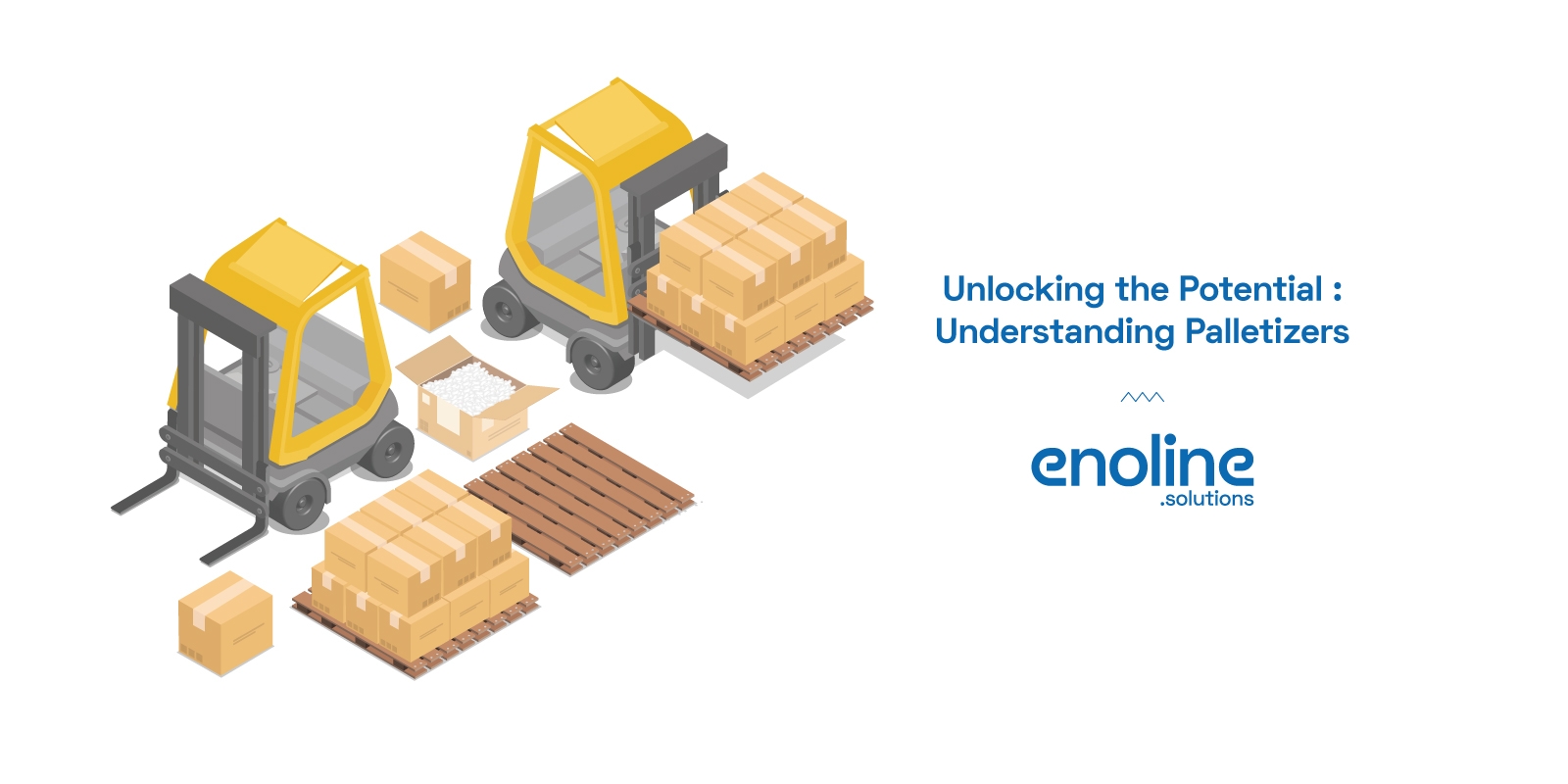
Palletizers are sophisticated machines designed to swiftly and methodically stack and arrange products onto pallets, ensuring optimal organization and efficiency within warehouse operations.
Enhancing Safety and Efficiency: The Role of Palletizers
• Ensuring Product Safety: Palletizers play a crucial role in ensuring product safety and minimizing the risk of accidents during the palletizing process.
• Expedited Storage and Shipping: By streamlining the palletizing process, companies can expedite storage and shipping operations, minimizing delays and maximizing efficiency.
• Optimizing Warehouse Space: Palletizers enable companies to maximize the utilization of warehouse space, efficiently stacking goods in a safe and orderly manner.
Mechanics in Motion: Understanding Palletizer Operation
Palletizing product operation goes through a palletizing robotic arm equipped with clamps, which move vertically and horizontally to transport goods from storage points to pallets. These arms follow pre-established routes, positioning products on standard-sized pallets or according to programmed schemes. You can also have palletizing cell which works great and quickly as well.
Types of Palletizing machines
• Cartesian Palletizers: Ideal for high-intensity work speed and precise positioning, offering reliability and flexibility across various product types.
• Layered Palletizers: Suited for high-production environments, efficiently transferring entire product layers onto pallets for stability and compactness.
• Magnetic Head Palletizers: Designed for metal product palletizing, providing specialized solutions for specific material handling needs.
• Robotized Palletizers: Offering precision, speed, and flexibility, these solutions cater to diverse industry sectors with robust palletizing capabilities.
Embracing the Benefits: Why Invest in Palletizing Systems
Investing in palletizing systems yields significant economic and organizational advantages for companies managing pallet-intensive operations:
• Substantial Reduction in Personnel Expenses: Palletizers can reduce personnel expenses by up to 70%, optimizing labor costs.
• Cost Savings in Management: Companies can achieve cost savings of 35% through efficient palletizing systems, reducing overheads.
• Enhanced Workplace Safety: Palletizers contribute to a safer work environment by minimizing accidents and ensuring proper material handling.
• Boost in Productivity: With up to 30% increase in productivity, palletizing systems eliminate the need for constant staff supervision, improving operational efficiency.
• Reliable Execution: Palletizing systems ensure consistent execution times, providing companies with predictable workflow management.
• Space Optimization: Palletizers maximize warehouse space utilization, allowing companies to store and transport goods more efficiently.
Understanding Palletizers: Common Questions Answered
• What does a palletizer do?
A palletizer is a machine that efficiently stacks and organizes products onto pallets, facilitating streamlined warehouse operations and optimized storage and shipping processes.
• What are the different types of palletizers?
There are several types of palletizers, including Cartesian palletizers, pallet eur, layered palletizers, magnetic head palletizers, and robotized palletizers, each offering unique benefits and suitability for various industry requirements.
• What is a packaging palletizer?
A packaging palletizer is a type of palletizer specifically designed for the efficient stacking and arrangement of packaged products onto pallets, ensuring secure and stable loads for transportation and storage.
• How does palletizing work?
Palletizing involves the use of mechanical arms equipped with clamps to transport products from storage points to pallets. These arms follow predefined routes, positioning products according to programmed schemes or standard pallet configurations, thereby optimizing space and ensuring stability during transport and storage.
• What are the standard pallet sizes ?
The standard pallet height typically ranges from 5 to 6 inches (12.7 to 15.24 centimeters). This height is designed to accommodate the dimensions of most shipping containers and ensure stability during transportation and storage. However, pallet heights can vary depending on factors such as load capacity, industry requirements, and specific usage scenarios. It's essential for businesses to consider these factors when selecting pallets to optimize efficiency and safety within their supply chain operations.
Standard pallet sizes can vary depending on region and industry standards. However, some common dimensions include:
48 inches x 40 inches (1220 mm x 1020 mm): This is one of the most widely used pallet sizes in North America, commonly referred to as the GMA pallet or Grocery Manufacturers Association pallet.
42 inches x 42 inches (1070 mm x 1070 mm): Often used in industries such as pharmaceuticals, chemicals, and automotive, this square pallet size offers stability and compatibility with international shipping containers.
Euro Pallet (1200 mm x 800 mm) / Pallet eur: Standardized in Europe, this pallet size is widely used for transporting goods across the continent. It measures approximately 47.2 inches x 31.5 inches.
1200 mm x 1000 mm: Another common European pallet size, slightly larger than the Euro pallet, providing ample space for goods and facilitating efficient storage and transportation..
Understanding the various pallet sizes available allows businesses to select the most suitable option based on factors such as product dimensions, transportation methods, and warehouse space constraints.
Conclusion
Investing in palletizing technology empowers companies to streamline operations, enhance safety standards, and achieve significant cost savings, ultimately driving greater efficiency and competitiveness in the market.
If you are looking for fast and reliable palletizing equipment, contact us to get a fast and free palletizer quotation !
Let us find the best palletizers for your company !