June 21st
Palletizers: Enhancing Efficiency in Material Handling and Packaging
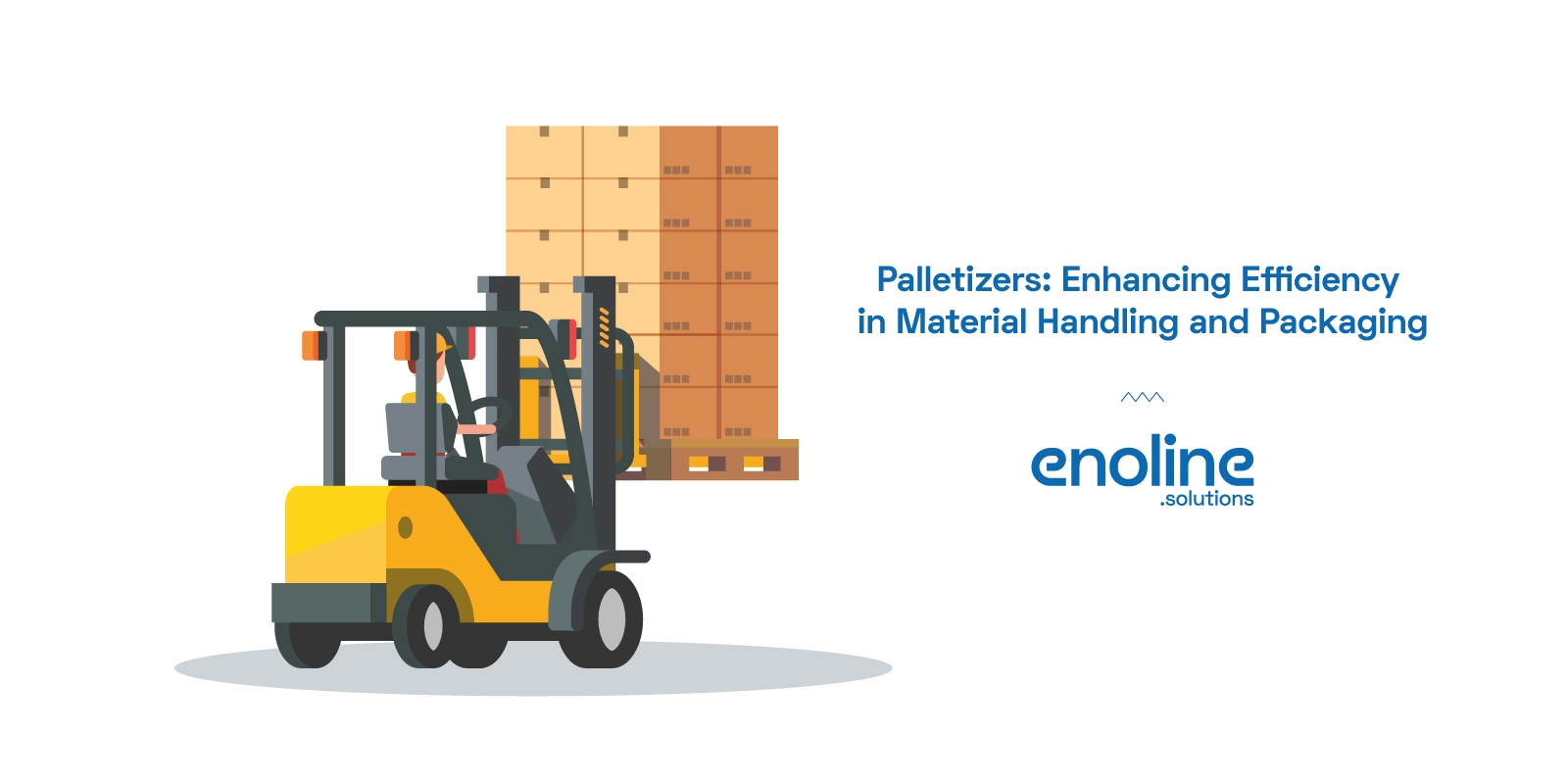
Chapter 1: What is a Palletizer and How Does It Work?
A palletizer is an advanced automated material handling machine that plays a crucial role in stacking and arranging individual products into cohesive loads. By streamlining the handling, storage, and shipment processes, palletizers offer a convenient and cost-effective solution. These machines are an integral part of larger packaging systems, where they often incorporate various functions such as weighing, counting, sorting, labeling, metal detection, and wrapping. Some of these functions may be integrated into the palletizing machine itself, while others can be performed by separate equipment.
Palletizers leverage the concept of unit load, which involves combining multiple materials to facilitate efficient handling. Instead of moving several small individual items, it is more efficient and economical to transport a large, single unit. Finished goods, which are typically packaged in boxes, cases, trays, or crates, are consolidated into a single unit supported by pallets or roll cages. The former is known as a secondary unit load, while the latter is referred to as a tertiary unit load.
The products are stacked by the palletizer onto a pallet, giving rise to its name. Pallets, made of wood, plastic, paper, or steel, are flat and stable structures with notches or openings that facilitate lifting and moving using forklifts or hand pallet trucks. Depending on the design, pallets can have either two-way or four-way forklift entry. Most pallets can handle loads of up to one ton and have an area of approximately one square meter. Here are some standard pallet dimensions:
• North America: 1016 x 1219 mm (40.0 x 48.00 in), with 3.7% unused floor space in ISO containers.
• Europe, Asia: 1000 x 1200 mm (39.37 x 47.24 in), with 6.7% unused floor space.
• Australia: 1165 x 1165 mm (45.9 x 45.9 in), with 8.1% unused floor space.
• North America, Europe, Asia: 1067 x 1067 mm (42.00 x 42.00 in), with 11.5% unused floor space.
• Asia: 1100 x 1100 mm (43.30 x 43.30 in), with 14% unused floor space.
• Europe: 800 x 1200 mm (31.50 x 47.24 in), with 15.2% unused floor space.
In addition to pallets, some palletizers can also stack items on slip sheets or conveying surfaces. These variations are known as unitizers, and they eliminate the need for pallets. While the terms "palletizers" and "unitizers" are sometimes used interchangeably, they represent distinct approaches to load consolidation.
Chapter 2: A Brief History of Palletizers
The origins of palletizers can be traced back to the early 20th century when manual hand stacking was the primary method for organizing pallet loads. However, as the need for faster and more efficient logistics emerged, new material handling and storage capabilities became imperative. During World War 2, pallets and pallet handling gained immense importance, paving the way for advancements in this field.
The first mechanical palletizer, developed by Lamson Corp. in 1948, was a row-forming palletizer. It featured an area where materials were arranged in rows before being transferred to the pallet. This innovation significantly reduced manual labor and increased stacking efficiency.
As technology continued to advance, more sophisticated palletizers were developed. In the 1960s, the introduction of robotic palletizers revolutionized the industry. These automated machines utilized robotic arms to handle and stack products with precision and speed. Robotic palletizers offered flexibility in handling various product sizes and shapes, making them highly versatile for different industries.
With the advent of computerized systems in the 1980s, palletizers became even more advanced. The integration of computer-controlled operations allowed for precise programming and customization of stacking patterns. This level of automation improved efficiency, reduced errors, and increased overall productivity in material handling and packaging processes.
In recent years, palletizers have continued to evolve to meet the demands of modern supply chains. They have become more intelligent and interconnected, incorporating technologies such as artificial intelligence (AI) and the Internet of Things (IoT). These advancements enable real-time data monitoring, predictive maintenance, and optimization of palletizing operations.
Chapter 3: Types of Palletizers
Palletizers come in various types, each designed to cater to specific packaging needs and production requirements. Here are some commonly used types of palletizers:
1. Conventional Palletizers:
Also known as high-level palletizers, these machines typically operate at elevated heights. They receive products from a conveyor system and arrange them into stable loads using mechanical arms, vacuum grippers, or clamps. Conventional palletizers are suitable for handling heavy loads and high-speed production lines.
2. Robotic Palletizers:
These palletizers employ robotic arms equipped with end-of-arm tools (EOAT) to pick up, position, and stack products. Robotic palletizers offer flexibility in handling various product sizes and configurations. They can be easily reprogrammed to adapt to changing production needs and can integrate with other equipment in the packaging line.
3. Layer Palletizers:
Layer palletizers are specifically designed to stack products in complete layers onto pallets. They excel at handling cases, trays, or other containers that are arranged in uniform layers. Layer palletizers often use mechanical pushers or sweep arms to slide entire layers onto the pallets.
4. Mixed-Load Palletizers:
These palletizers are capable of handling multiple product types simultaneously, allowing for the creation of mixed pallet loads. Mixed-load palletizers are commonly used in distribution centers where products with different shapes, sizes, and packaging configurations need to be consolidated onto a single pallet.
5. Bag Palletizers:
Bag palletizers specialize in stacking bags of various materials, such as cement, flour, pet food, or fertilizer. They often incorporate features like bag flattening, bag turning, and bag conditioning to ensure stable and tightly packed loads.
6. Depalletizers:
Although not strictly a type of palletizer, depalletizers are worth mentioning as they perform the reverse function. Depalletizers are used to unload products from pallets, commonly found in industries such as beverage bottling and container filling.
Here is our best selling palletizer page, discover more.
Chapter 4: Benefits of Palletizers
The implementation of palletizers offers numerous benefits to industries involved in material handling and packaging:
1. Increased Efficiency:
Palletizers significantly improve stacking speed and accuracy compared to manual labor. They can handle large volumes of products consistently, reducing the time required for packaging and shipment preparation.
2. Labor Savings:
Automated palletizers reduce reliance on manual labor, resulting in cost savings and improved worker safety. Employees can be reassigned to more skilled tasks, enhancing overall productivity.
3. Space Optimization:
Compact Palletizers enable efficient use of storage and transportation space. By consolidating products into unit loads, they maximize the use of pallets and reduce wasted space.
4. Product Protection:
Palletizers ensure proper stacking and secure loads, minimizing the risk of product damage during transportation and storage. This helps preserve product quality and reduces the likelihood of returns or customer complaints.
5. Flexibility and Adaptability:
With programmable operations and versatile end-of-arm tools, palletizers can handle a wide range of product sizes, shapes, and packaging configurations. They can be easily adjusted to accommodate changes in production requirements.
6. Data Monitoring and Analysis:
Advanced palletizers equipped with IoT capabilities enable real-time data monitoring and analysis. This information can be used to identify bottlenecks, optimize operations, and implement predictive maintenance practices.
Conclusion
Palletizers have come a long way since their inception, evolving from simple manual devices to highly sophisticated automated systems. These machines have revolutionized material handling and packaging processes, offering increased efficiency, labor savings, and improved product protection. With ongoing advancements in technology, palletizers continue to adapt to the changing needs of industries, providing versatile solutions for stacking products onto pallets. Whether it's a conventional palletizer, a robotic system, or a specialized bag palletizer, these machines play a crucial role in optimizing supply chains and ensuring the smooth flow of goods from production to distribution.
Let us find the best palletizing solution for your business !