May 19th
Boost Your Production Efficiency with the Monoblock Machine
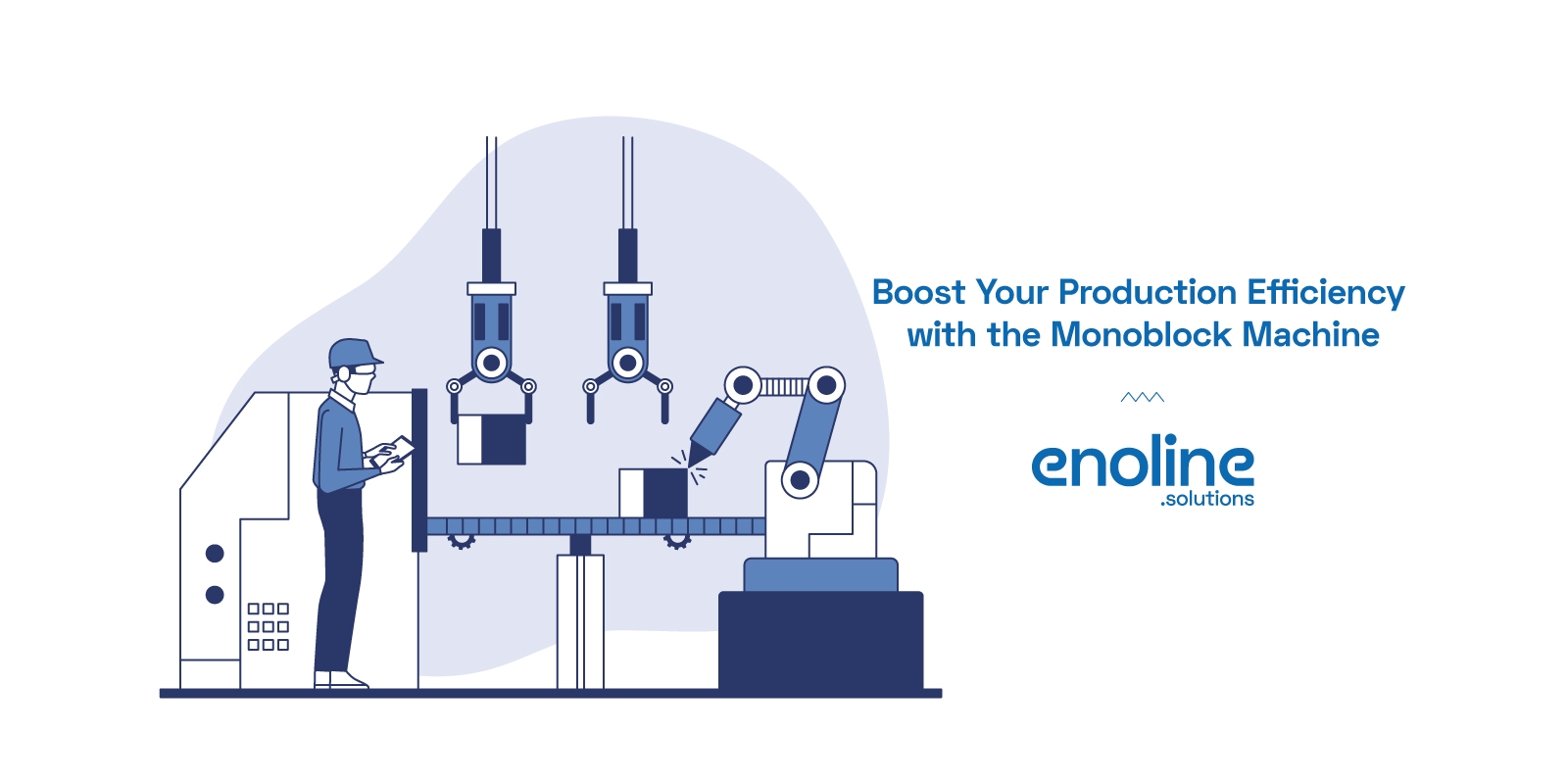
Introduction
In today's fast-paced manufacturing industry, optimizing production efficiency is crucial for businesses to stay competitive. The monoblock machine is a cutting-edge technology that offers a streamlined solution for various manufacturing processes. This article will explore the benefits, functionalities, and applications of the monoblock machine, providing you with valuable insights to enhance your production capabilities.
What is a Monoblock Machine?
A monoblock machine is an advanced piece of manufacturing equipment that integrates multiple functions into a single unit. It combines different stages of the production process, eliminating the need for manual transfer between individual machines. This all-in-one design enhances operational efficiency and reduces downtime, resulting in increased productivity.
Advantages of Using a Monoblock Machine
Utilizing a monoblock machine offers several advantages for manufacturers seeking to optimize their operations. Let's explore the key benefits of incorporating this innovative technology:
Streamlined Workflow:
The monoblock machine eliminates the time-consuming process of moving products between various machines, reducing the risk of errors and improving overall workflow efficiency.
Space Optimization:
With its compact design, the monoblock machine requires less floor space compared to multiple individual machines. This frees up valuable factory space for other essential operations.
Cost Efficiency:
By consolidating multiple functions into a single unit, the monoblock machine helps reduce initial investment costs and lowers operational expenses associated with maintenance, energy consumption, and labor.
Enhanced Product Quality:
The seamless integration of processes in a monoblock machine minimizes product handling, resulting in better quality control and reduced chances of contamination or damage during production.
Increased Output:
The continuous and automated workflow of the monoblock machine allows for higher production volumes, enabling manufacturers to meet growing demands efficiently.
Applications of Monoblock Machines
Monoblock machines have a wide range of applications across various industries due to their versatility and adaptability. Let's explore some common sectors where these machines are utilized:
Pharmaceutical Industry:
Monoblock machines play a vital role in the pharmaceutical industry, where they are used for processes such as tablet and capsule production, blending, filling, and packaging. These machines ensure precise and efficient handling of pharmaceutical products, maintaining the highest quality standards.
Food and Beverage Industry:
In the food and beverage industry, monoblock machines are employed for the production of beverages, sauces, oils, and other consumable goods. They excel in tasks such as filling, capping, labeling, and packaging, offering fast and reliable automation to streamline the production process.
Cosmetics and Personal Care:
Monoblock machines find extensive usage in the cosmetics and personal care industry. They enable the efficient filling, capping, and packaging of products like lotions, creams, perfumes, and makeup items. The integration of multiple functions in a single unit enhances productivity and ensures consistent product quality.
Chemical and Cleaning Solutions:
Monoblock machines are utilized in the chemical industry for the production of cleaning solutions, detergents, and other chemical products. These machines handle tasks such as liquid filling, sealing, and labeling, ensuring precise measurements and minimizing product wastage.
Automotive and Industrial:
In the automotive and industrial sectors, monoblock machines contribute to the production of lubricants, oils, adhesives, and other fluids. They provide efficient filling, capping, and labeling capabilities, meeting the specific requirements of these industries and facilitating streamlined production processes.
Healthcare and Medical Devices:
Monoblock machines are employed in the healthcare and medical device industry for processes such as filling and packaging of syringes, vials, ampoules, and other medical products. The high precision and sterility requirements are met with the advanced features and stringent quality control mechanisms of these machines.
Home Care Products:
Manufacturers of home care products like detergents, cleaning solutions, and air fresheners rely on monoblock machines for efficient production. These machines handle the filling, capping, and labeling processes, ensuring accurate measurements, consistent quality, and seamless packaging.
Nutraceuticals and Dietary Supplements:
Monoblock machines find application in the nutraceutical and dietary supplement industry, where they are used for filling capsules, tablets, powders, and liquids. These machines enable precise dosage control, effective sealing, and reliable packaging, ensuring product integrity and compliance with regulatory standards.
Pet Care Products:
Monoblock machines are also utilized in the production of pet care products such as shampoos, conditioners, and veterinary medicines. They offer efficient filling, capping, and labeling capabilities, allowing manufacturers to meet the diverse needs of pet owners while maintaining product quality and safety.
Other Industries:
Additionally, monoblock machines have applications in industries like household products, personal hygiene, agricultural chemicals, and more. Their versatility and ability to integrate multiple processes make them a valuable asset in optimizing production efficiency across various sectors.
By harnessing the capabilities of monoblock machines, manufacturers can streamline their production processes, increase output, maintain product quality, and gain a competitive edge in their respective industries.
How Does a Monoblock Machine Work?
A monoblock machine operates through a synchronized process that combines multiple functions seamlessly. Here's a step-by-step overview of how this advanced equipment works:
Product Feeding:
The raw materials or products are loaded into the monoblock machine's input section, either manually or through an automated system.
Processing and Transformation:
The monoblock machine carries out the required processes, such as filling, labeling, capping, sealing, or any other manufacturing steps, based on its specific configuration and intended application.
Quality Control:
Throughout the production cycle, the monoblock machine incorporates quality control mechanisms to ensure the output meets the desired standards. This may include inspections, measurements, and other quality assurance procedures.
Packaging and Output:
Once the product has undergone all necessary processing and quality checks, the monoblock machine proceeds to package the finished goods. It can handle various packaging materials, sizes, and formats, such as bottles, tubes, pouches, or cartons.
Product Discharge:
The completed and packaged products are then discharged from the monoblock machine, ready for distribution or further processing.
Key Features and Components
Monoblock machines are equipped with several key features and components that contribute to their efficiency and functionality. Here are some notable elements commonly found in these machines:
Control Panel:
The control panel allows operators to monitor and control the machine's operation, adjust settings, and troubleshoot any issues.
Conveyor System:
A conveyor system facilitates the smooth movement of products within the monoblock machine, ensuring a continuous workflow.
Filling Mechanism:
Depending on the application, monoblock machines may include volumetric, gravimetric, or piston filling mechanisms to accurately dispense the required amount of product.
Capping and Sealing Units:
These units ensure proper sealing and closure of containers, preventing leakage or contamination.
Labeling Systems:
Monoblock machines can incorporate labeling systems for applying product labels, batch numbers, expiry dates, or other required information.
Sensors and Detectors:
Integrated sensors and detectors help identify any anomalies during the production process, such as missing caps, incorrect fill levels, or product defects.
Safety Features:
Monoblock machines prioritize operator safety and often include features like emergency stop buttons, safety guards, and interlocking mechanisms to prevent accidents.
Selecting the Right Monoblock Machine
When choosing a monoblock machine for your specific production needs, consider the following factors:
Production Capacity:
Determine the required production volume per unit of time to ensure the chosen monoblock machine can meet your output goals.
Product Specifications:
Assess the size, shape, and properties of your products to ensure the monoblock machine is compatible and capable of handling them effectively.
Flexibility and Customization:
Evaluate whether the machine can be easily adjusted or customized to accommodate different product variations, packaging formats, or future production requirements.
Ease of Operation and Maintenance:
Look for user-friendly interfaces, clear documentation, and easily accessible components to simplify machine operation and maintenance tasks.
Supplier Reputation and Support:
Choose a reputable supplier known for delivering high-quality equipment and providing reliable after-sales support, including technical assistance and spare parts availability.
We have 30+ years of experience in the packaging industry, we are here to help you chose the perfect monoblock machine you need, contact us for a fast and free quote !
Maintenance and Care
Proper maintenance and care are crucial for the optimal performance and longevity of your monoblock machine. Follow these guidelines:
Regular Cleaning:
Clean the machine regularly, removing any product residue or debris to prevent contamination and ensure smooth operation.
Scheduled Inspections:
Conduct routine inspections to identify any signs of wear and tear, loose connections, or damaged components. Address any issues promptly to avoid further damage.
Lubrication:
Follow the manufacturer's recommendations for lubrication to ensure the machine's moving parts operate smoothly. Regularly check and replenish lubricants as needed.
Training and Operator Awareness:
Train operators on proper machine operation, maintenance procedures, and safety protocols. Encourage them to report any abnormalities or concerns promptly.
Spare Parts Inventory:
Maintain an inventory of commonly used spare parts to minimize downtime. Replace worn-out or damaged parts with genuine replacements from the machine's manufacturer. We have more than 400k+ parts in stock in our Warehouse (North America).
Manufacturer's Guidelines:
Adhere to the manufacturer's guidelines for maintenance schedules, recommended cleaning agents, and specific care instructions for your monoblock machine model.
FAQs
What is the monoblock machine used for?
The monoblock machine is used for integrating multiple manufacturing processes into a single unit, reducing manual handling and increasing production efficiency. It finds applications in various industries such as pharmaceuticals, food and beverages, cosmetics, and more.
How does the monoblock machine improve production efficiency?
The monoblock machine improves production efficiency by eliminating the need for manual transfer between individual machines, reducing downtime and the risk of errors. It streamlines the workflow, enhances product quality, and increases output volume.
Is the monoblock machine suitable for small-scale operations?
Yes, monoblock machines are available in different sizes and configurations, making them suitable for both large-scale and small-scale operations. They can be customized to meet specific production requirements and space limitations.
Can a monoblock machine be customized for specific production requirements?
Yes, monoblock machines can be customized to accommodate specific production needs. Manufacturers can tailor the machine's functionalities, such as filling, capping, labeling, and packaging, to suit their products and processes.
What are the safety measures to consider when operating a monoblock machine?
When operating a monoblock machine, it's important to follow safety protocols and guidelines. This includes wearing appropriate personal protective equipment, understanding emergency stop procedures, and ensuring proper training for machine operation.
What is the maintenance schedule for a monoblock machine?
The maintenance schedule for a monoblock machine varies depending on factors such as usage, operating conditions, and manufacturer recommendations. Regular cleaning, inspections, lubrication, and addressing issues promptly are key elements of maintaining a monoblock machine.
Conclusion
Incorporating a monoblock machine into your production line can revolutionize your manufacturing processes, leading to enhanced efficiency, increased productivity, and improved product quality. By eliminating manual transfer between machines and integrating multiple functions into a single unit, monoblock machines streamline operations and optimize output. Remember to follow proper maintenance and care guidelines to ensure the longevity and optimal performance of your monoblock machine.
Let us find the best monoblock machine for your business !