August 28th
Essential Maintenance and Troubleshooting for Packaging Machines
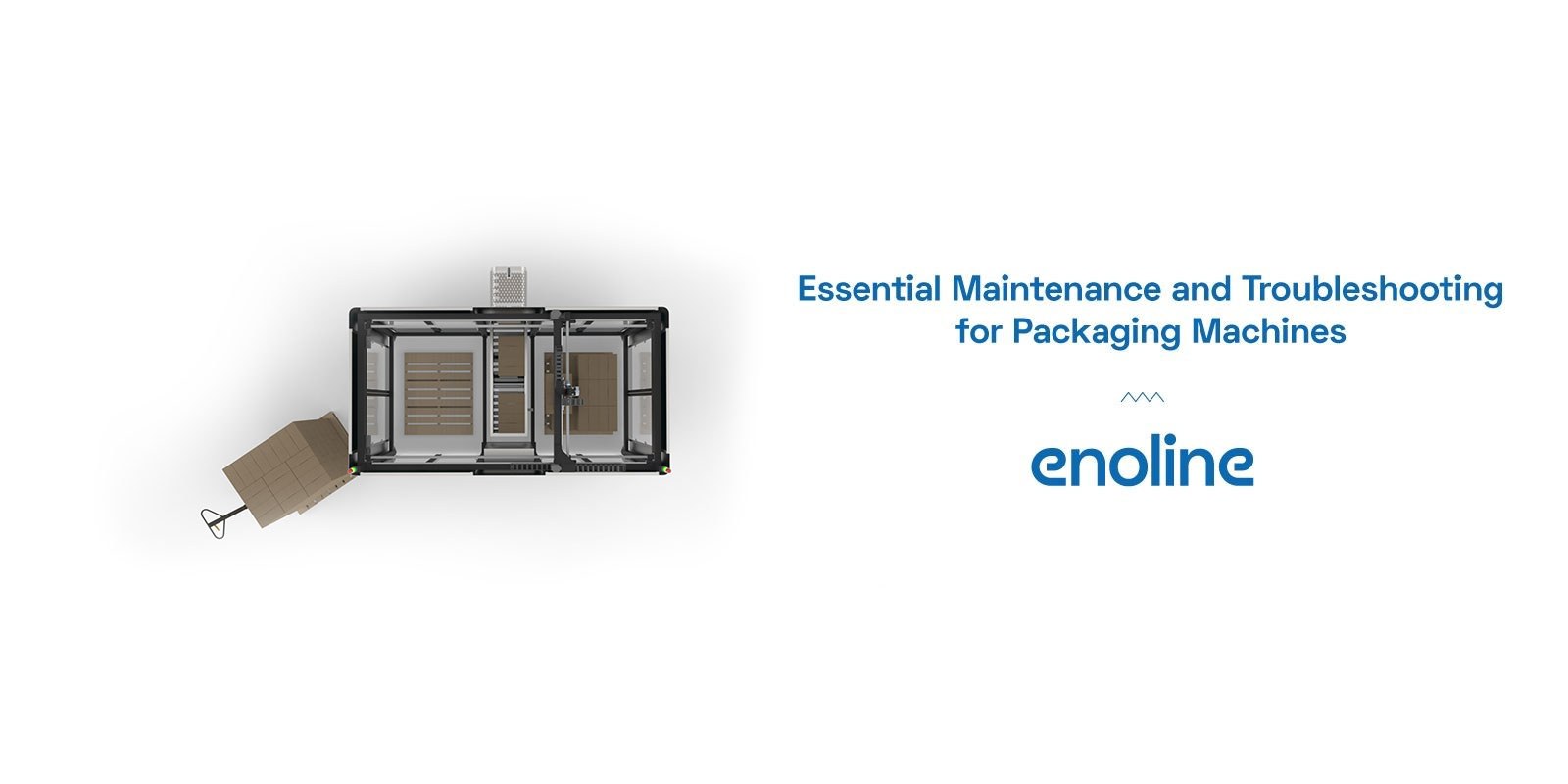
Packaging machines are vital to the smooth operation of production lines across various industries. Regular maintenance and timely troubleshooting are crucial for preventing costly downtime and ensuring that these machines operate efficiently. This article provides a comprehensive guide to preventative maintenance for packaging equipment and offers practical advice for solving common issues.
Preventative Maintenance for Packaging Equipment
1. The Importance of Regular Maintenance
Preventative maintenance is essential for extending the lifespan of packaging machines and minimizing unexpected breakdowns. By regularly inspecting and servicing your equipment, you can catch potential issues before they become major problems, reducing the risk of downtime and ensuring continuous production. Regular maintenance also helps in maintaining the efficiency and safety of the machines, contributing to a consistent product quality.
2. Developing a Maintenance Schedule
Creating a maintenance schedule tailored to the specific needs of your packaging machines is crucial. This schedule should include routine tasks such as cleaning, lubrication, inspection, and calibration. The frequency of these tasks will depend on the machine's usage, the environment in which it operates, and the manufacturer's recommendations. For instance, machines operating in dusty environments may require more frequent cleaning and filter replacement.
3. Training for Maintenance Personnel
Proper training for maintenance personnel is critical to ensure that preventative maintenance is carried out effectively. Staff should be familiar with the operation manuals of the machines, understand the importance of regular maintenance, and know how to perform basic troubleshooting. Investing in regular training and refresher courses can significantly reduce the likelihood of maintenance-related errors.
4. Using Quality Spare Parts
When parts need to be replaced during maintenance, it is essential to use high-quality, manufacturer-approved spare parts. Using substandard or incompatible parts can lead to premature wear and tear, reducing the efficiency of the machine and potentially causing further damage. Always keep an inventory of commonly replaced parts to minimize downtime during maintenance.
5. Documentation and Record-Keeping
Maintaining detailed records of all maintenance activities is important for tracking the history of the machine's performance and identifying recurring issues. This documentation should include the date of each maintenance task, the parts replaced, and any observations made during the inspection. Keeping accurate records helps in planning future maintenance and making informed decisions about machine upgrades or replacements.
Common Issues with Packaging Machines and How to Solve Them
1. Inconsistent Packaging Quality
One of the most common issues with packaging machines is inconsistent packaging quality, which can manifest as improper sealing, uneven fills, or misaligned labels. This problem is often caused by incorrect machine settings, worn-out components, or contamination within the machine. To solve this, check and adjust the machine settings, replace any worn parts, and ensure the machine is clean and free of debris. Regular calibration can also help maintain consistent performance.
2. Machine Jams and Downtime
Jams can cause significant downtime, disrupting production schedules and increasing costs. Common causes of machine jams include misfed materials, worn belts, or improper tension settings. To resolve jams, first, stop the machine and safely clear the jammed material. Inspect the feeding mechanism, belts, and tension settings to identify and correct the root cause. Regular inspection and timely replacement of worn parts can help prevent jams from occurring.
3. Equipment Overheating
Overheating is another common issue that can lead to machine failure if not addressed promptly. Causes of overheating may include inadequate ventilation, excessive load, or malfunctioning cooling systems. To prevent overheating, ensure that the machine has sufficient airflow, avoid overloading it, and regularly inspect and maintain the cooling systems. Installing temperature monitoring devices can also help detect overheating early and prevent serious damage.
4. Electrical and Control System Failures
Electrical issues, such as faulty wiring or control system failures, can halt production and cause extensive downtime. Regularly inspect the electrical components for signs of wear, corrosion, or loose connections. Ensure that all control systems are functioning correctly and update software or firmware as needed. Having a qualified technician on hand to troubleshoot and repair electrical problems can minimize downtime.
5. Pneumatic and Hydraulic Issues
Many packaging machines rely on pneumatic or hydraulic systems to operate. Leaks, pressure drops, or faulty valves in these systems can lead to performance issues. Regularly inspect hoses, fittings, and seals for leaks, and check pressure levels to ensure they meet the manufacturer's specifications. Replacing worn or damaged components promptly can prevent system failures and maintain efficient operation.
6. Noise and Vibration Problems
Excessive noise or vibration during operation is often a sign of underlying mechanical issues, such as unbalanced components, loose bolts, or misaligned parts. To address these problems, inspect the machine for loose or worn components and make necessary adjustments or replacements. Balancing rotating parts and ensuring proper alignment can reduce noise and vibration, leading to smoother operation and prolonged machine life.
7. Software Glitches and User Interface Errors
Modern packaging machines are often equipped with sophisticated software and user interfaces. Glitches or errors in these systems can disrupt production and lead to incorrect machine operation. Regularly update the software to the latest version provided by the manufacturer, and ensure that operators are trained to handle any interface issues. If problems persist, contacting the manufacturer's technical support team may be necessary to resolve software-related issues.
Conclusion
Proper maintenance and timely troubleshooting are essential for ensuring the efficient and reliable operation of packaging machines. By following the preventative maintenance practices outlined in this article, you can minimize the risk of downtime, extend the lifespan of your equipment, and maintain high product quality. Additionally, being prepared to address common issues quickly will help you keep your production line running smoothly and avoid costly disruptions.
Let us find the best packaging machine for your company !